Circularity in ceramics
︎︎︎ Abandoned Earth Plate Series
This tableware uses the “Recycled Glaze” made from the sawdust of natural stones, another invention by Studio Peipei. Shop︎︎︎
The ceramics industry is tied to many different resources, none of which can be extracted sustainably or treated in a recyclable manner. This is because the raw materials extracted by mining and shipped around the world are fused together in the process. They cannot be separated and reused. So how can we work sustainably in ceramics?
The studio has analysed and revised the process based on the production of its own small series.
![]()
01 Waste is a system failure
In order to source clay from the region, the studio looked for a durable and meaningful solution. In doing so, it came across a source of waste from a nearby retailer: dried-out clay from damaged packaging. The thin foils tear very quickly, making the goods unusable for the time being. Any damage in the packaging, no matter how small, leads to the goods being sorted out. In a few weeks, several hundred kilos can accumulate, which exceeds the needs of the studio. With a little water, time and preparation, the material is like new and can be processed as usual.
The studio has analysed and revised the process based on the production of its own small series.
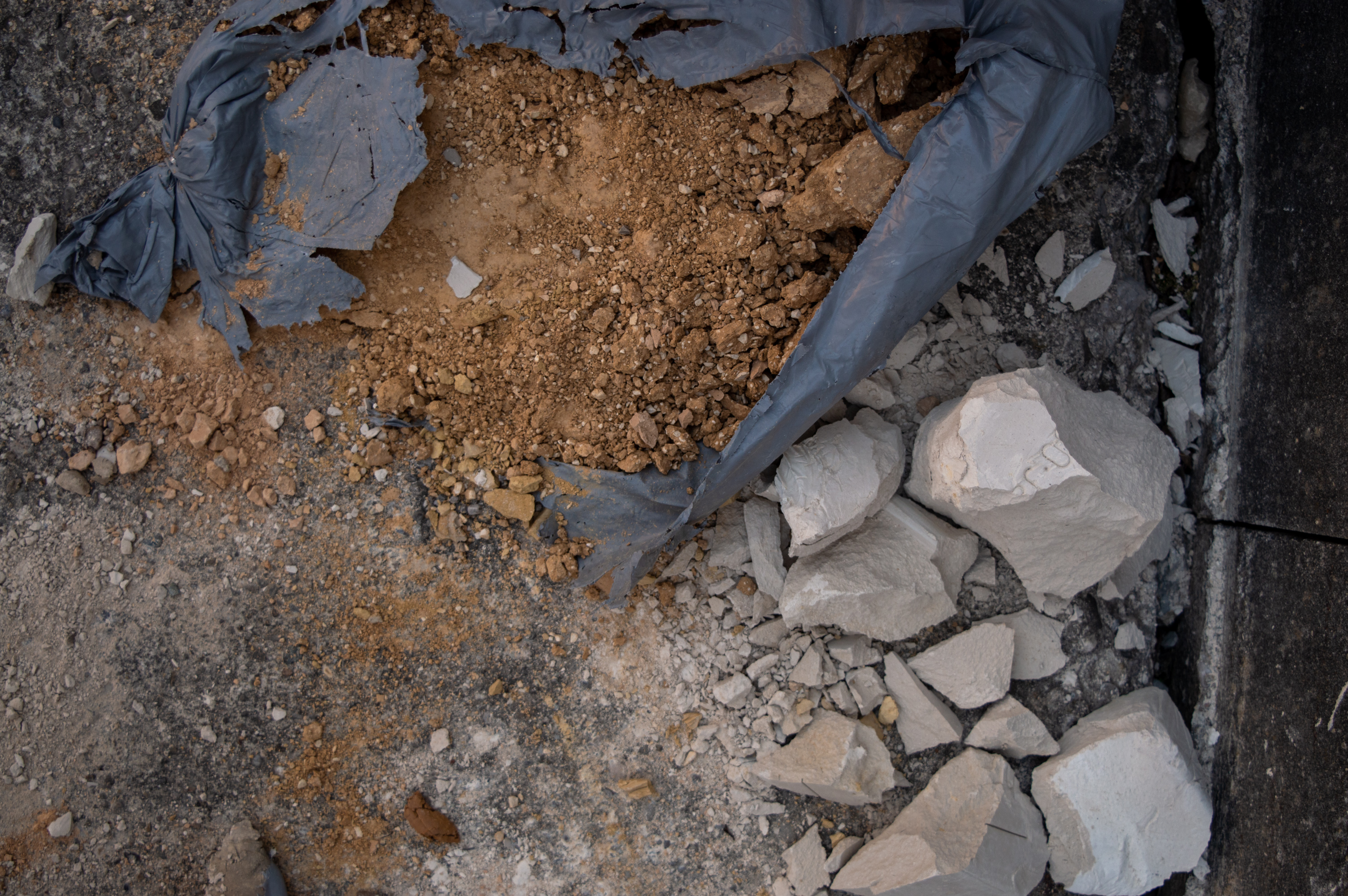
In order to source clay from the region, the studio looked for a durable and meaningful solution. In doing so, it came across a source of waste from a nearby retailer: dried-out clay from damaged packaging. The thin foils tear very quickly, making the goods unusable for the time being. Any damage in the packaging, no matter how small, leads to the goods being sorted out. In a few weeks, several hundred kilos can accumulate, which exceeds the needs of the studio. With a little water, time and preparation, the material is like new and can be processed as usual.
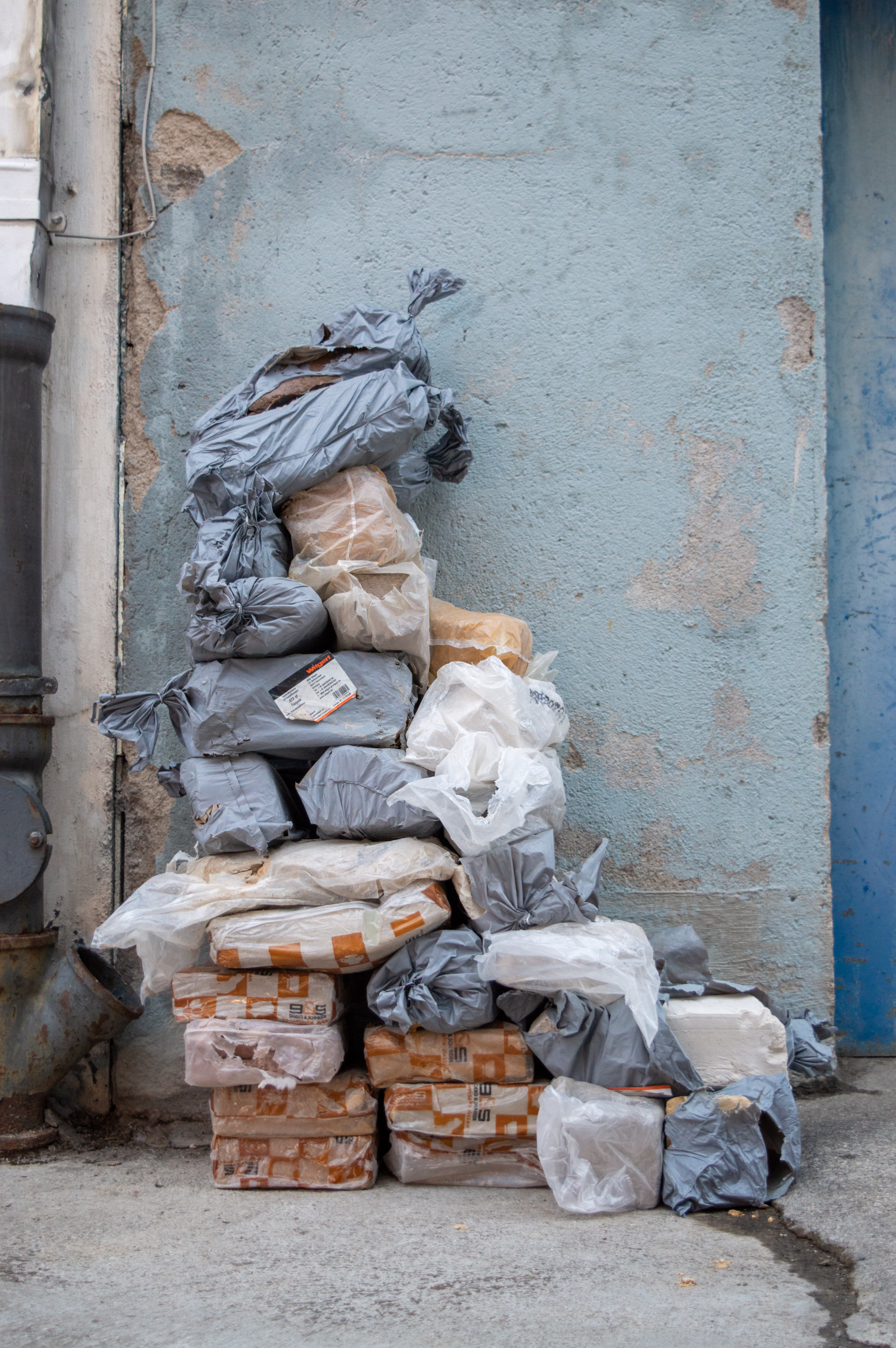

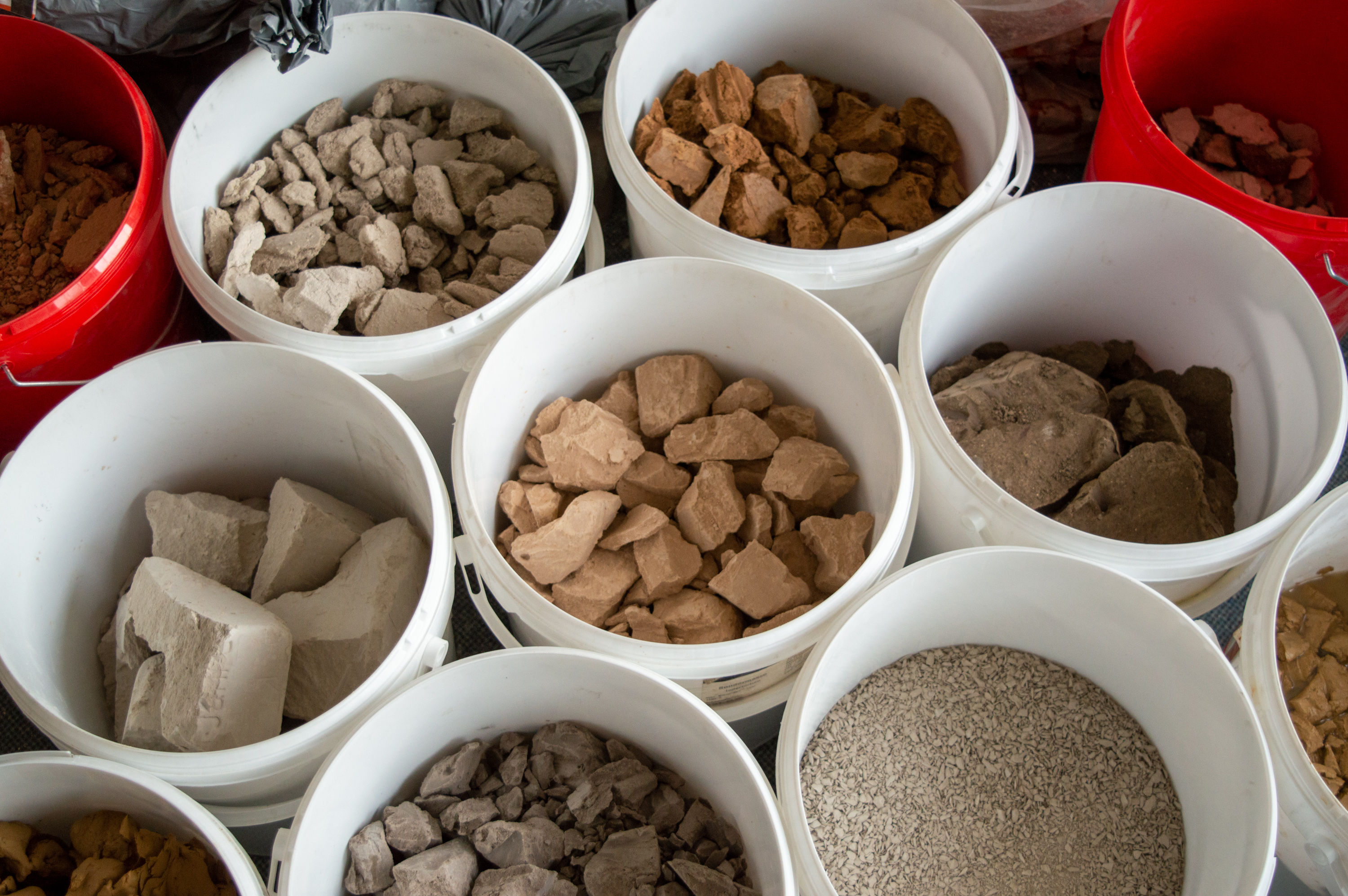
02 Water management
Even in a region with high precipitation such as southern Germany, the economical use of water must be integrated into every step. The studio not only collects and filters rainwater, but also used water, small quantities of which are constantly produced in the ceramic process. This is used to prepare the dried clay, mix glazes and much more.
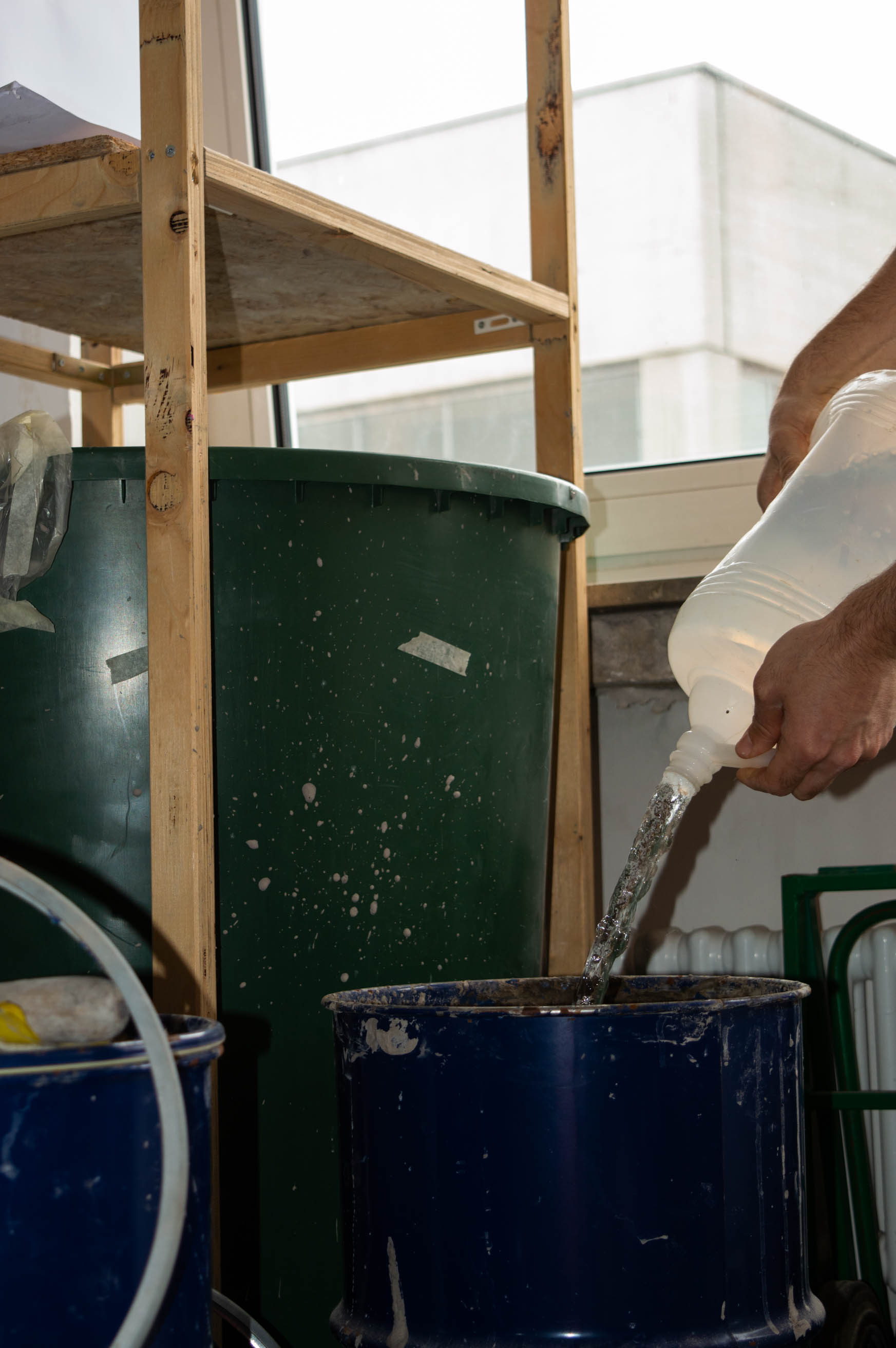
There are many techniques for producing ceramic products. Plaster moulds, for example, produce very precise series products, but unfortunately the production of plaster is very energy-intensive and the moulds are not very durable. Over time, they can no longer absorb water properly and have to be replaced.
“Application of natural gypsum for calcined gypsum production results in 140.7 kg CO2/t.”
[Carbon footprint analysis of calcined gypsum production in the Czech Republic, Journal of Cleaner Production, 2018]
A much better way is therefore a turntable or the ceramic 3D printing process. However, in the interests of the most minimalist solution, electricity was also avoided wherever possible. After some experimentation, the studio decided to only use internal remnants as an aid. A simple shape made of paper and plastic scraps resulted in a surprisingly efficient tool for producing simple plates.[Carbon footprint analysis of calcined gypsum production in the Czech Republic, Journal of Cleaner Production, 2018]

04 Firing
Of course, firing is the biggest ecological weak point. And it is just as clear that, for cost reasons alone, every kiln is always filled as efficiently as possible and every firing is carried out as sensibly as possible. Studio Peipei uses a small kiln that is powered by domestic electricity. In the long term, there are plans to experiment with feeding in solar power, which couldn’t be tested yet.
However, one simple option is to adapt the products precisely to the kiln size so that it can be filled as efficiently as possible. And gaps are filled with small products. Once again, form follows function.
Of course, firing is the biggest ecological weak point. And it is just as clear that, for cost reasons alone, every kiln is always filled as efficiently as possible and every firing is carried out as sensibly as possible. Studio Peipei uses a small kiln that is powered by domestic electricity. In the long term, there are plans to experiment with feeding in solar power, which couldn’t be tested yet.
However, one simple option is to adapt the products precisely to the kiln size so that it can be filled as efficiently as possible. And gaps are filled with small products. Once again, form follows function.
05 Recycling of remnants
When using different types of clay, there are always small pieces left over at the end, which are no longer enough for a plate. These leftovers are integrated into each product, which gives the range a striking look and gives the products a unique appearance.
When using different types of clay, there are always small pieces left over at the end, which are no longer enough for a plate. These leftovers are integrated into each product, which gives the range a striking look and gives the products a unique appearance.
Sorted out, raw clay is of course returned directly to the processing process. Waste material that has already been fired is crushed and added back to the raw clay as fireclay, which is only possible thanks to the internal preparation of the clay types. Just the biscuit fragments are used here, which make the ceramic products more robust and durable.
Glazed fragments are also crushed but collected separately. They are part of new, experimental glazes for workshops and other product series.
During this process, the studio developed a waste-based glaze that was released as its own product to make a sustainable product available to everyone.

07 Fundamentals
An object with a background story will always be treated with much more care and therefore last longer than a faceless mass product. As a society, we need to relearn to appreciate the value of things instead of preferring interchangeable and readily available items.
An object with a background story will always be treated with much more care and therefore last longer than a faceless mass product. As a society, we need to relearn to appreciate the value of things instead of preferring interchangeable and readily available items.
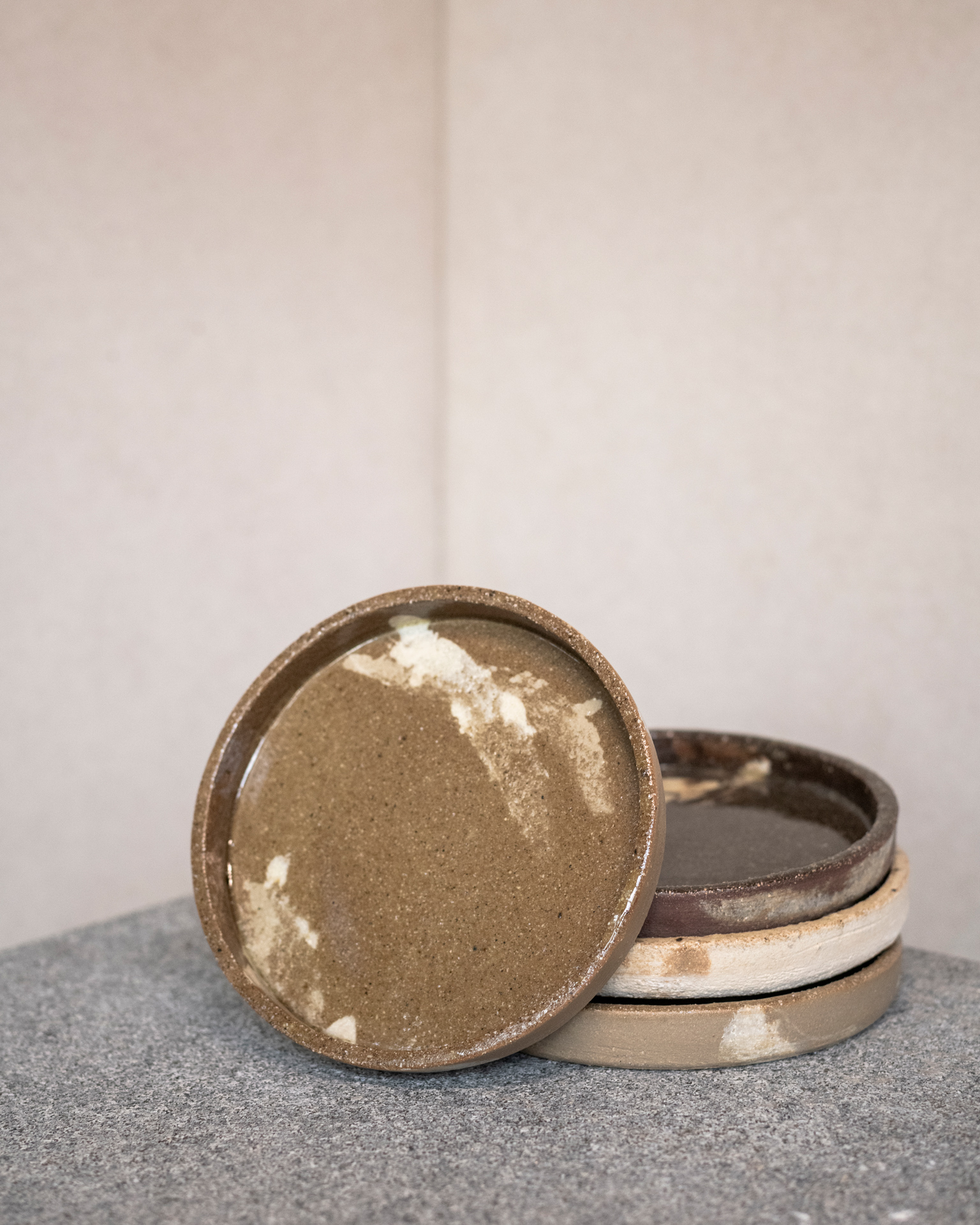
Foto by Matthias Ziemer

