Recycled glaze
︎︎︎ From the sawdust of natural stones
The ceramics industry consumes a large amount of different raw materials and yet is less in the spotlight than other sectors, such as the construction or automotive industries. In fact, all three need the same resources, for example cobalt, iron, copper, quartz sand, limestone and much more.
A brief insight into the destructive extent of mines can be found here︎︎︎. These “strategic raw materials” are being fought over ever more fiercely, as it has become clear how dependent entire countries are on them. The switch to sustainable solar energy, for example, will greatly increase the demand for copper, a resource that simply produces greenish to turquoise colors in a glaze and is then forever fused with other ingredients. On the one hand, this raises the question of what is more important, and on the other, it shows how everything is connected.
The main ingredient in this “recycled glaze” is the sawdust from the Dichtl company in Southern Germany (62%), only 60km from the studio. We also use dust from Barbany Artesans in Barcelona when there is a shortage, as the winter in southern Germany is too cold for stone work. A wonderful side effect of this collaboration is that we are using the dust from the figures that adorn the Sagrada Familia.
The processing of the various natural stones also produces large quantities of stone dust, which could not be used so far. Up to 40 tons per month are deposited at each production site. This glaze gives the „waste“ a further task for the first time and thus replaces many valuable resources. Thanks to our meticulous examination of natural stones, we can dispense with many common additives such as metal oxides, ball clay, bone ash, kaolin and much more. Perhaps the biggest milestone is that this glaze does not require quartz sand: The main ingredient in most common glazes. Stones already contain enough quartz. In addition, we only need two more ingredients, which also come from Germany and therefore from our immediate surroundings.
![]()
It is more urgent than ever that all sectors work together
to create local material cycles. This project aims to set a good example
and encourage others to follow the same direction.
![]()
![]()
Ceramic object by Elena Krafftto create local material cycles. This project aims to set a good example
and encourage others to follow the same direction.

The main ingredient in this “recycled glaze” is the sawdust from the Dichtl company in Southern Germany (62%), only 60km from the studio. We also use dust from Barbany Artesans in Barcelona when there is a shortage, as the winter in southern Germany is too cold for stone work. A wonderful side effect of this collaboration is that we are using the dust from the figures that adorn the Sagrada Familia.
The processing of the various natural stones also produces large quantities of stone dust, which could not be used so far. Up to 40 tons per month are deposited at each production site. This glaze gives the „waste“ a further task for the first time and thus replaces many valuable resources. Thanks to our meticulous examination of natural stones, we can dispense with many common additives such as metal oxides, ball clay, bone ash, kaolin and much more. Perhaps the biggest milestone is that this glaze does not require quartz sand: The main ingredient in most common glazes. Stones already contain enough quartz. In addition, we only need two more ingredients, which also come from Germany and therefore from our immediate surroundings.
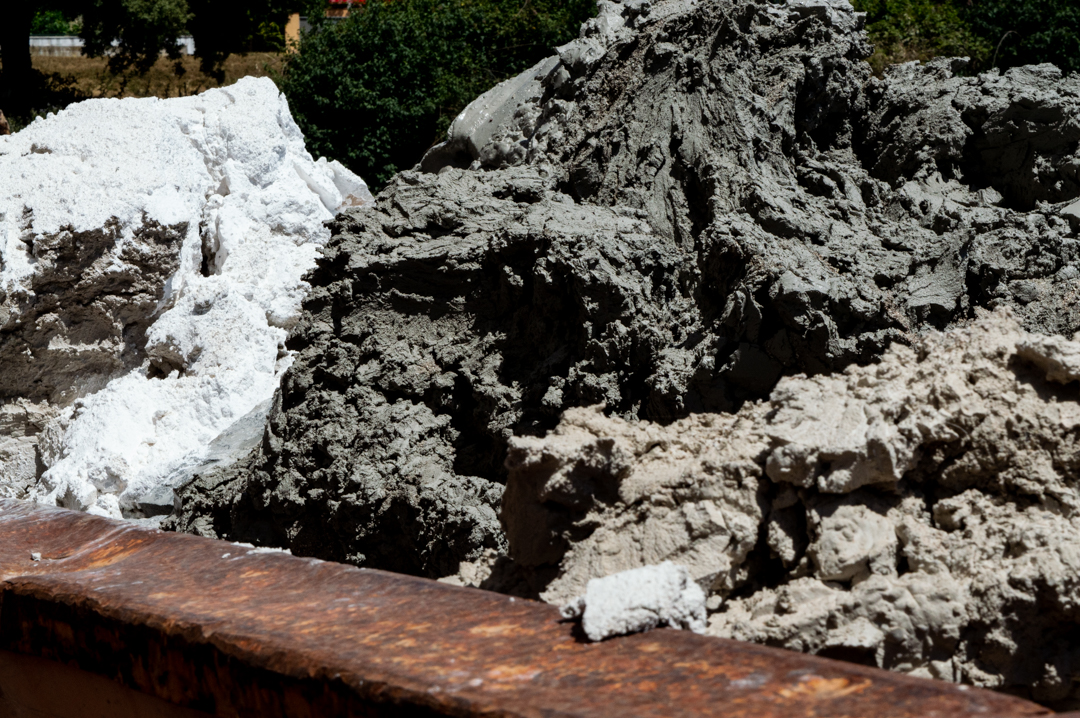
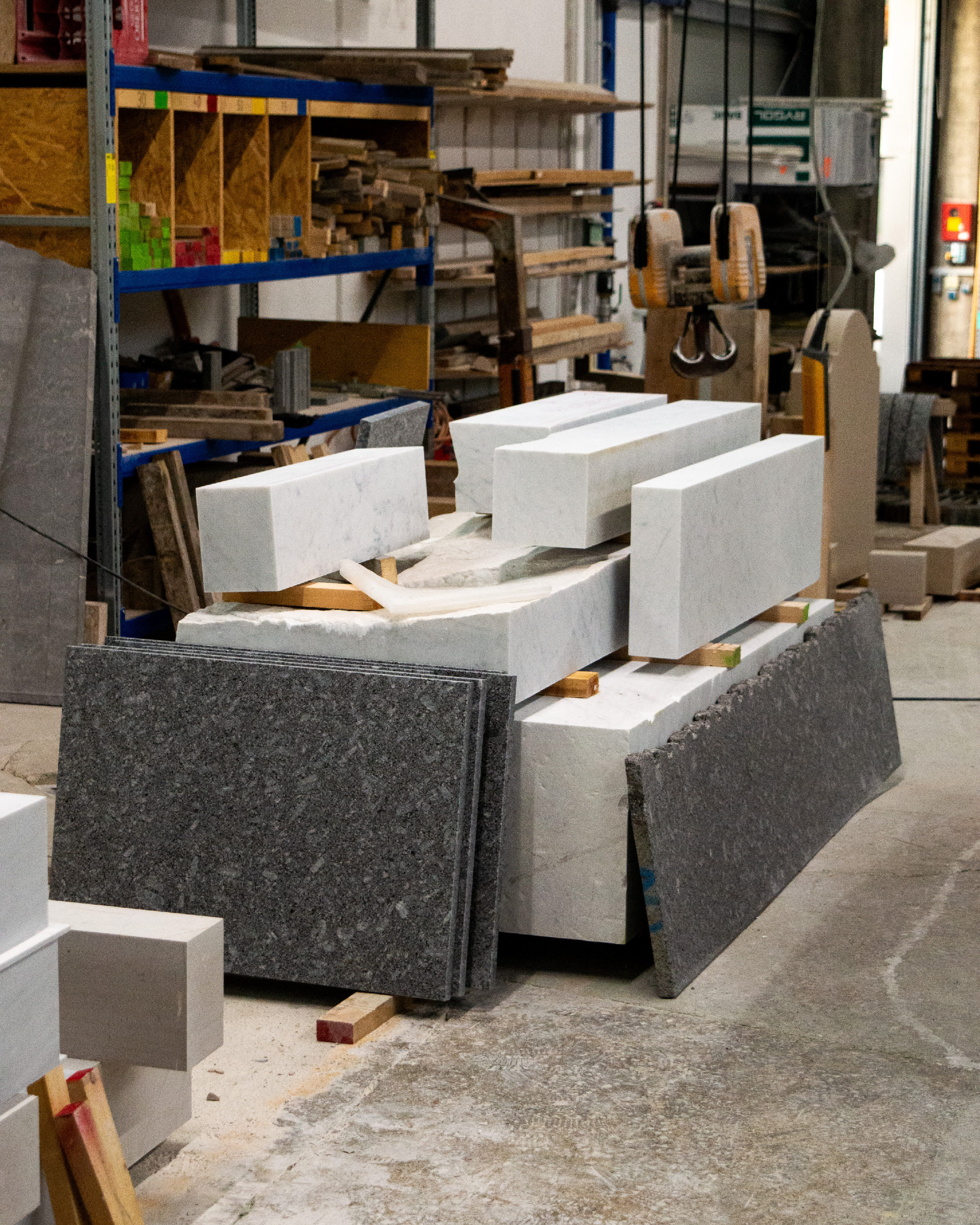

Another advantage is that the water required for processing is already pressed out of the stone dust in the production facilities. Originally to comply with landfill regulations. But as luck would have it, the dust is thus perfectly prepared for us and enables us to produce very quickly and with low energy consumption in just a few steps.
Thanks to our extensive research,
it is possible to use perfectly prepared waste materials that are available on site.
it is possible to use perfectly prepared waste materials that are available on site.

When used separately, the individual types of stone produce very different colors and surface textures in a glaze. However, in the interests of efficient waste recycling, we use the mixed stone dust, which has a relatively constant appearance due to the predominantly common types of stone.


In addition to recycling raw materials, packaging is also a big issue.
This glaze is intended to solve one problem, not open another.
That's why responsibility is taken into account here at various levels. The following detailed packaging solutions are only possible thanks to a versatile network and motivated people from our environment who point us to secondary resources. This glaze is intended to solve one problem, not open another.
The labels were printed in collaboration with
thehappyclub.de︎︎︎
, a local risography studio that uses a low-energy printing process with plant-based ink.
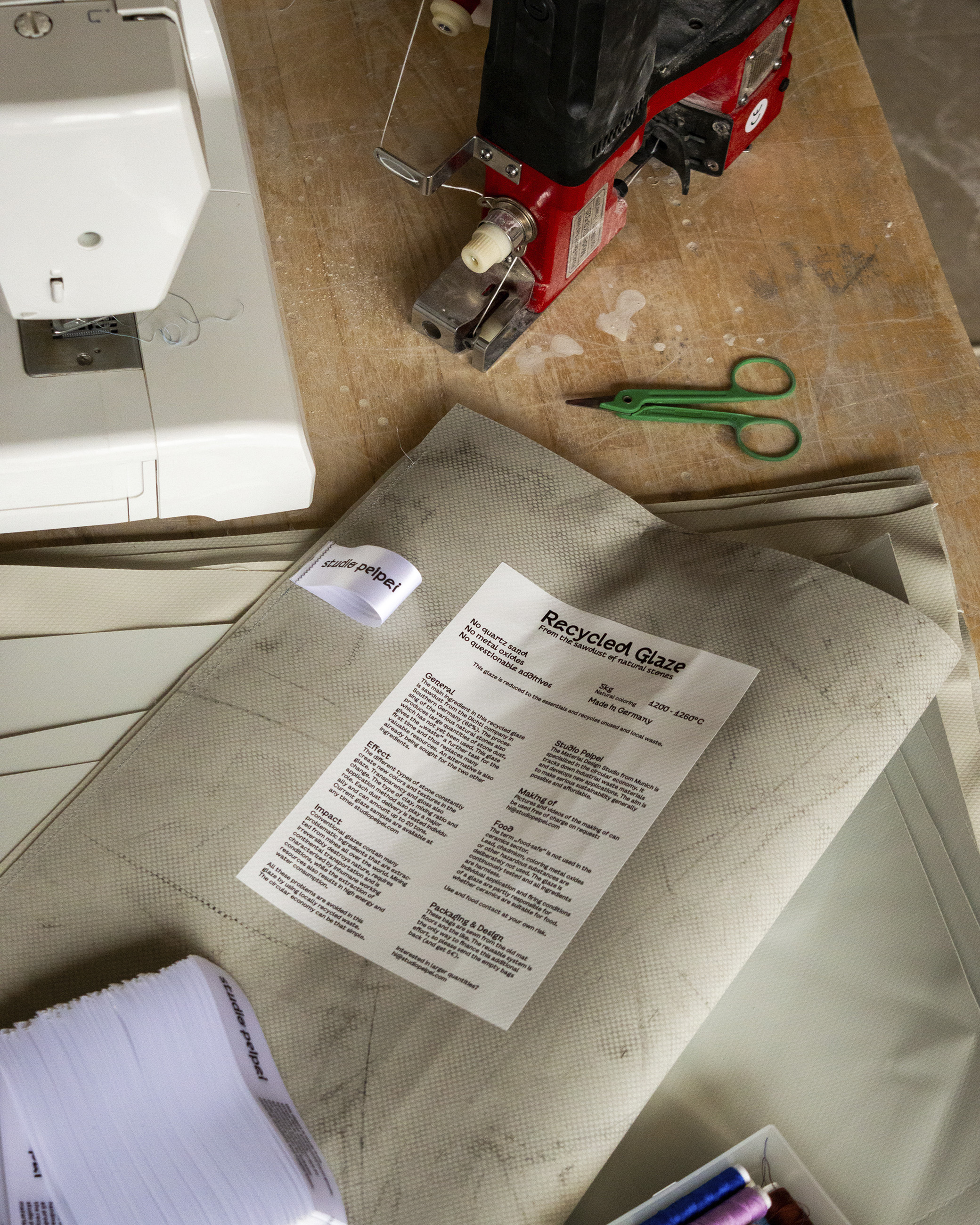
Reuse of old tarpaulins and advertising banners for larger 5kg packagings. In addition to smaller leftovers, the first major donation came from the local climbing hall Boulderwelt Muc Ost︎︎︎. They donated around 100 sqm of old mat flooring.

Uncoated paper pouches, 100% recycled and recyclable.

Ceramic object by Tanya Koch


Colorful dots in the glaze are created by fine pieces of stone that slip through the sieving process. This effect only occurs sporadically and is then only visible on light-colored clays.